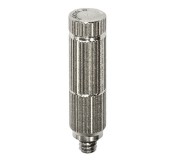
The main component of all misting systems is the nozzles, regardless of whether they operate at low or high pressure. When choosing a nozzle, there is only one decisive factor: how effective the spraying is and how fine the mist particles are.
The Physics of Misting
The physics behind the misting process is simple. Purified water, free of impurities and salts, is supplied to the nozzles under high pressure ranging from 7 to 100 bar via a pump. Each nozzle consists of several parts:
- Flow straightener or vortex insert, which helps to stabilize the water flow and eliminate turbulence.
- Filters.
- Anti-drip valve, which stops the water flow when the pump is turned off. It consists of a spring-loaded pin or ball.
- Sealing rings.
- Nozzle head with an orifice.
The body and head of the nozzle are made of nickel-plated brass or stainless steel. The lifespan of the orifice largely depends on the material it is made from. The most durable nozzles are those where the orifice is directly built into the stainless steel head. These are also the most expensive. More commonly, tungsten carbide, aluminum, or silicon inserts are used. Corundum (synthetic ruby) inserts are particularly effective, as they have a perfect spray pattern, high strength, and exceptional wear resistance, maintaining their geometry even after five years of operation.
An Important Consideration: Water Quality
Another critical factor is that the orifice diameter is extremely small—ranging from 0.10 to 1.0 mm. If the water contains high levels of iron or salts, these tiny holes can easily become clogged, and even a built-in filter will not help. Therefore, only properly treated water should be used.
Differences Between High-Pressure and Low-Pressure Misting Nozzles
High-pressure misting nozzles do not differ significantly from low-pressure ones, but there are some key distinctions:
- High-pressure nozzles must operate at a minimum of 30 bar, as the anti-drip valve will not open otherwise. The orifice diameter ranges from 0.15 mm to 0.5 mm.
- Low-pressure nozzles have larger orifices, ranging from 0.3 mm to 1.0 mm, and their valves open at 1-2 bar.
Applications of Misting Nozzles
The particle size (dispersion) of the mist is determined by the orifice diameter:
- Larger diameters are used for dust suppression in factories, greenhouses, and stores.
- Smaller diameters are used in offices and outdoor cafés to increase humidity and reduce temperature.
When choosing misting nozzles, pay attention to the spray pattern. If the spray is uneven, it means that water streaks will flow from one side instead of forming a fine mist, resulting in puddles under the nozzle.
Common Mistakes and How to Avoid Them
If low-quality nozzle inserts are used, high pressure will enlarge their orifices within a few months, causing them to spray water droplets instead of mist. This will lead to excessive water consumption and premature pump wear.
To avoid disappointment with misting technology, it is better to invest a little more in high-tech products from reputable brands rather than buying cheap, low-quality imitations.